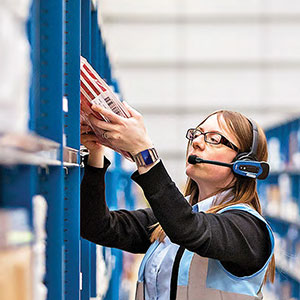
Combat labor challenges to create an engaged and productive workforce
Technology enables and supports workers
Finding and retaining labor is one of the biggest challenges today’s supply chains face. It is a job seeker’s market, as businesses struggle to fill vacancies to keep their warehouses and transportation networks running smoothly.
Supply chain organizations across industries need to rethink labor management – from boosting motivation to reduce turnover, to training temporary employees for success during peak seasons, to complying with continually changing health & safety guidelines – all while improving productivity.
Key takeaways
What the survey shows, and what we can learn from it
Only 37% of respondents have sufficient staff
Hiring and retaining employees remains a key challenge for businesses, but leading organizations are in better shape - 89% have enough staff
versus 3% of advanced supply chains can fully onboard employees in a day or less
With short onboarding and training times, leading organizations face fewer delays before employees become fully productive
achieve their warehouse safety goals, as opposed to only 29% of advanced organizations
Employee health and comfort is critical to reducing churn, and leading organizations are significantly ahead
Getting started
It is increasingly difficult to attract workers into an environment that can be both physically demanding, and occasionally dangerous. Creating a safe, engaging workplace will enable supply chain managers to retain and motivate their staff.
How does your supply chain measure up?
Take this rapid self-assessment: gain instant insights and start determining priorities.
Our self-assessment takes just a minute to complete. It will help you determine how your supply chain performs and how it compares against other organizations. It also recommends which areas to focus on first.
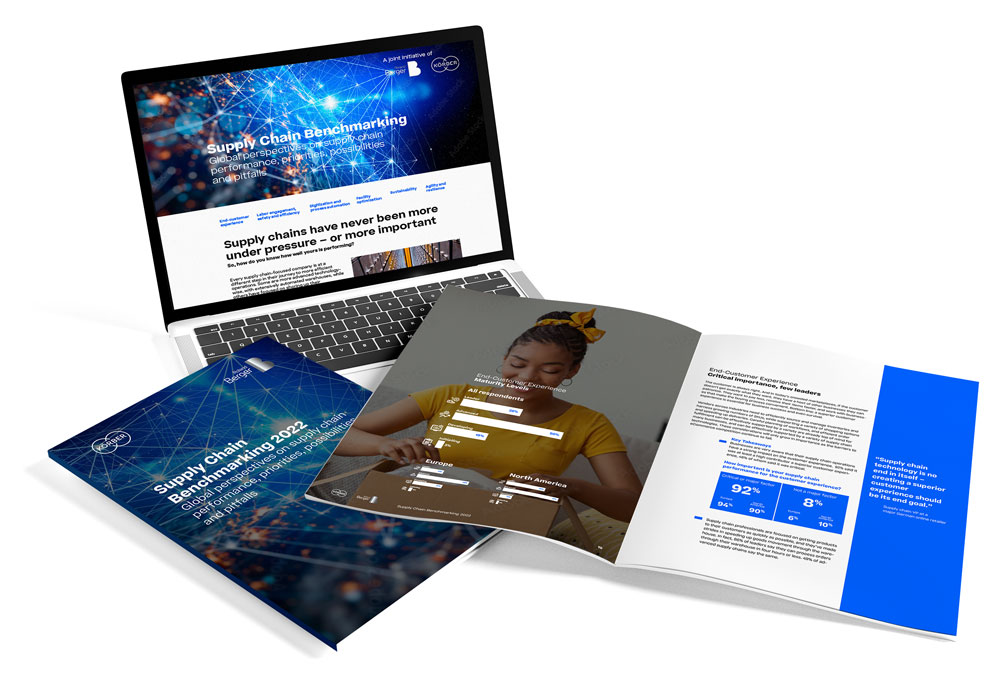
About the supply chain benchmarking report
In late 2021, Körber Supply Chain commissioned international strategy consultancy Roland Berger to survey supply chain professionals across North America and Europe. Its goal was to benchmark the progress that companies are making against the six complexity factors. Based on their survey responses, respondents were grouped into four maturity levels: